在工業(yè)自動化領(lǐng)域,2D視覺檢測技術(shù)憑借其成熟性、高性價比和廣泛適用性,始終是外觀檢測的核心手段之一。盡管近年來3D視覺技術(shù)快速發(fā)展,但2D視覺在平面缺陷檢測、高精度圖像分析和快速部署場景中仍占據(jù)不可替代的地位。本文將從技術(shù)原理、核心優(yōu)勢、應(yīng)用場景及優(yōu)化方向等角度,系統(tǒng)解析2D視覺外觀檢測的現(xiàn)狀與發(fā)展。
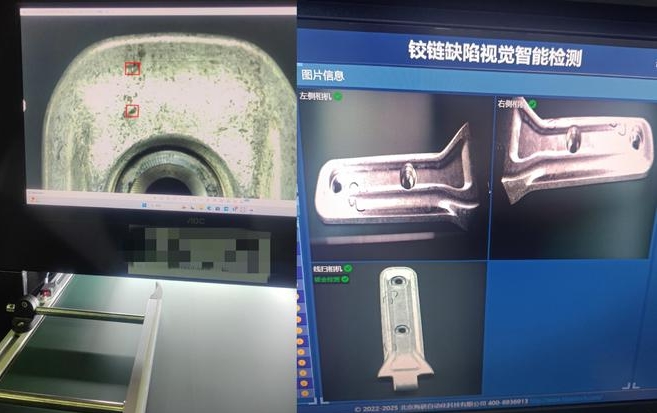
一、2D視覺檢測的技術(shù)原理與核心優(yōu)勢2D視覺檢測基于平面圖像采集與分析技術(shù),通過高分辨率相機捕捉物體表面圖像,結(jié)合算法處理提取特征信息(如顏色、紋理、形狀等),并與預(yù)設(shè)標(biāo)準(zhǔn)進行比對,從而識別缺陷或異常。其核心優(yōu)勢體現(xiàn)在以下方面:
高精度平面檢測:適用于印刷質(zhì)量、標(biāo)簽完整性、表面劃痕等平面缺陷的識別,精度可達微米級,尤其在低反光材質(zhì)(如紙張、塑料)檢測中表現(xiàn)優(yōu)異。
快速響應(yīng)與低成本:2D系統(tǒng)硬件成熟,部署周期短,且成本顯著低于3D方案,適合中小型企業(yè)的產(chǎn)線改造需求。
靈活的場景適配:通過調(diào)整光源和算法,可適應(yīng)不同光照條件和材質(zhì)表面,例如通過偏振濾光鏡抑制高反光干擾,或通過多幀圖像融合提升復(fù)雜環(huán)境下的檢測穩(wěn)定性。
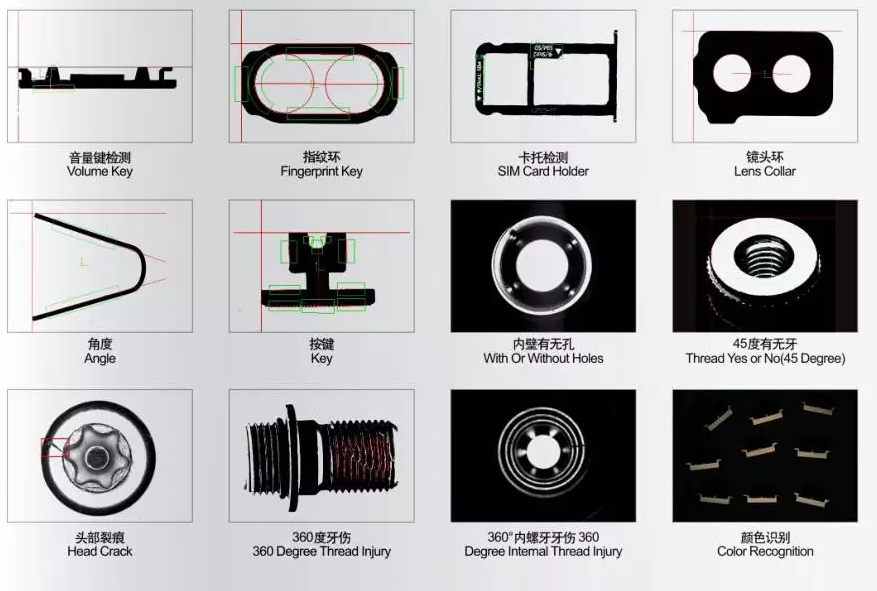
二、典型應(yīng)用場景與案例2D視覺外觀檢測已滲透至多個工業(yè)領(lǐng)域,其典型應(yīng)用包括:
1.印刷與包裝行業(yè):檢測標(biāo)簽錯位、色彩偏差、印刷模糊等缺陷,確保產(chǎn)品外觀一致性。
2.電子制造:識別電路板焊點缺陷、元器件錯漏裝,或屏幕劃痕等表面瑕疵。
3.食品與醫(yī)藥:檢查包裝封口完整性、標(biāo)簽信息準(zhǔn)確性,避免因包裝缺陷導(dǎo)致的污染風(fēng)險。
4.汽車零部件:在低反光部件(如內(nèi)飾件、塑料外殼)中檢測臟污、劃痕或裝配錯誤。
5.紡織與材料:分析布料均勻性、色差或異物殘留,提升成品良率。
三、技術(shù)挑戰(zhàn)與優(yōu)化方向盡管2D視覺技術(shù)成熟,但在實際應(yīng)用中仍面臨以下挑戰(zhàn):
1.環(huán)境光干擾:強反光或動態(tài)光照易導(dǎo)致誤檢,需結(jié)合自適應(yīng)光源(如頻閃照明)與圖像增強算法優(yōu)化。
2.復(fù)雜表面檢測局限:對曲面、高度差異大的物體(如汽車高反光漆面)難以精準(zhǔn)建模,需與3D技術(shù)互補使用。
3.小樣本訓(xùn)練難題:傳統(tǒng)算法依賴大量標(biāo)注數(shù)據(jù),可通過遷移學(xué)習(xí)或結(jié)合傳統(tǒng)圖像處理技術(shù)(如邊緣檢測)降低數(shù)據(jù)需求。
優(yōu)化路徑:
智能化算法升級:引入深度學(xué)習(xí)模型(如卷積神經(jīng)網(wǎng)絡(luò))提升缺陷分類能力,并開發(fā)小樣本訓(xùn)練框架以降低數(shù)據(jù)成本。
硬件協(xié)同創(chuàng)新:采用多光譜相機或高動態(tài)范圍(HDR)成像技術(shù),擴展對復(fù)雜材質(zhì)的適應(yīng)性。
系統(tǒng)集成化設(shè)計:通過模塊化軟件平臺兼容多品牌相機與光源,支持快速部署與參數(shù)調(diào)整,降低用戶使用門檻。
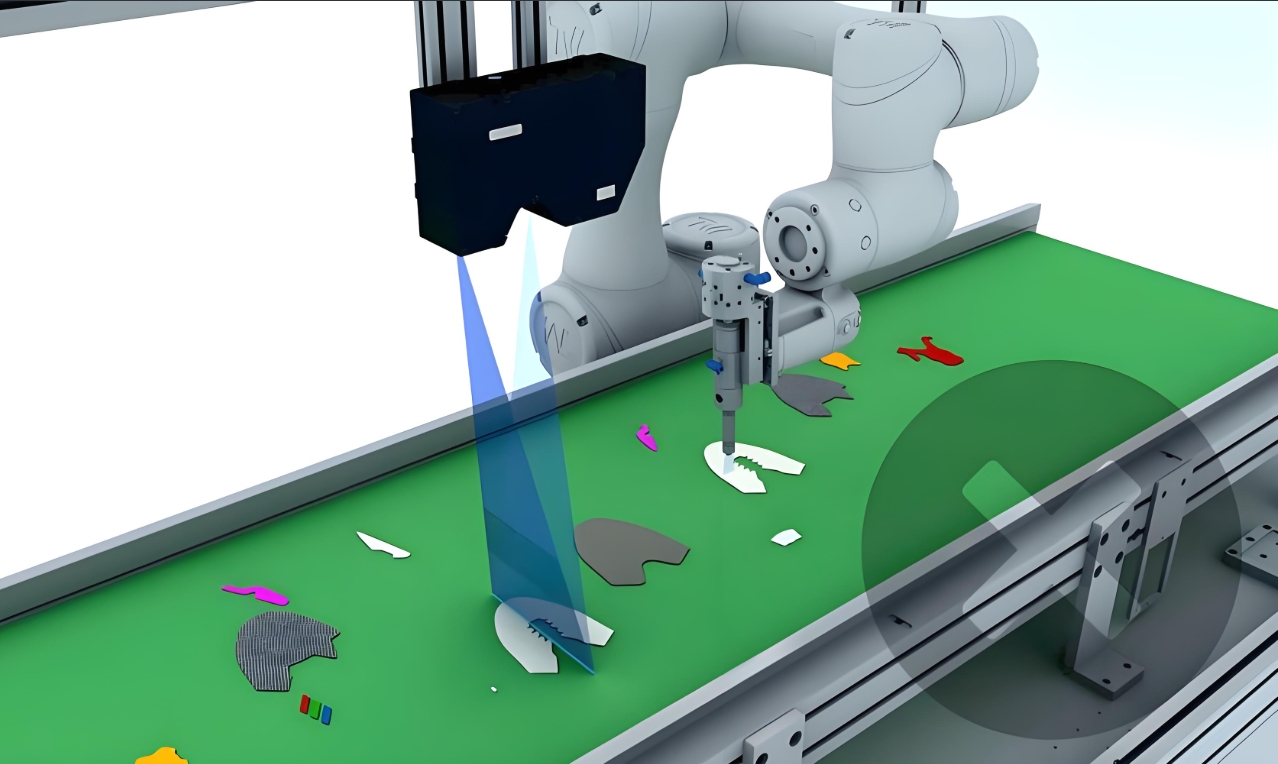
四、未來趨勢:與3D技術(shù)的融合與智能化升級 隨著工業(yè)檢測需求日益復(fù)雜,2D視覺正逐步與3D技術(shù)融合,形成混合解決方案。例如,在汽車制造中,2D用于平面缺陷檢測,3D則處理曲面尺寸測量,二者協(xié)同實現(xiàn)全維度質(zhì)量控制。此外,AI算法的引入(如實時缺陷分類、自適應(yīng)閾值調(diào)整)進一步提升了2D系統(tǒng)的智能化水平,使其在柔性生產(chǎn)線中更具競爭力。
結(jié)語 2D視覺外觀檢測技術(shù)作為工業(yè)自動化的基石,在成本敏感、平面檢測為主的場景中仍具不可替代性。通過算法優(yōu)化、硬件升級及與3D技術(shù)的協(xié)同,其應(yīng)用邊界將持續(xù)擴展,為制造業(yè)提供更高效、精準(zhǔn)的檢測支持。未來,隨著AI與邊緣計算技術(shù)的深度整合,2D視覺系統(tǒng)將向更智能、更柔性的方向演進,助力企業(yè)實現(xiàn)降本增效與質(zhì)量升級的雙重目標(biāo)。